In an increasingly competitive industrial environment, the ability to anticipate equipment failure is becoming a critical competitive advantage. This is all the truer in a fast-moving industry like pulp and paper, where every dollar counts.
The benefits of predictive maintenance are undeniable, especially in technology-intensive sectors such as paper production. Companies can reduce maintenance costs by up to 40% and minimize unplanned downtime thanks to intelligent monitoring technologies.
The subtle transformation of maintenance strategies
Traditionally, maintenance teams relied on reactive approaches. However, in a pulp and paper mill—where complex assets like digesters, refiners, and paper machines demand constant attention—this method often leads to substantial economic losses, mainly due to unanticipated downtime.
Today, remote monitoring technologies enable a proactive, prevention-focused approach. For example, vibration sensors on refiners can detect early signs of wear long before a catastrophic failure occurs.
The key challenge lies in making informed choices about these technologies and implementing them effectively. Unfortunately, companies sometimes prioritize cost over quality, which undermines the efficiency and reliability of their monitoring systems.
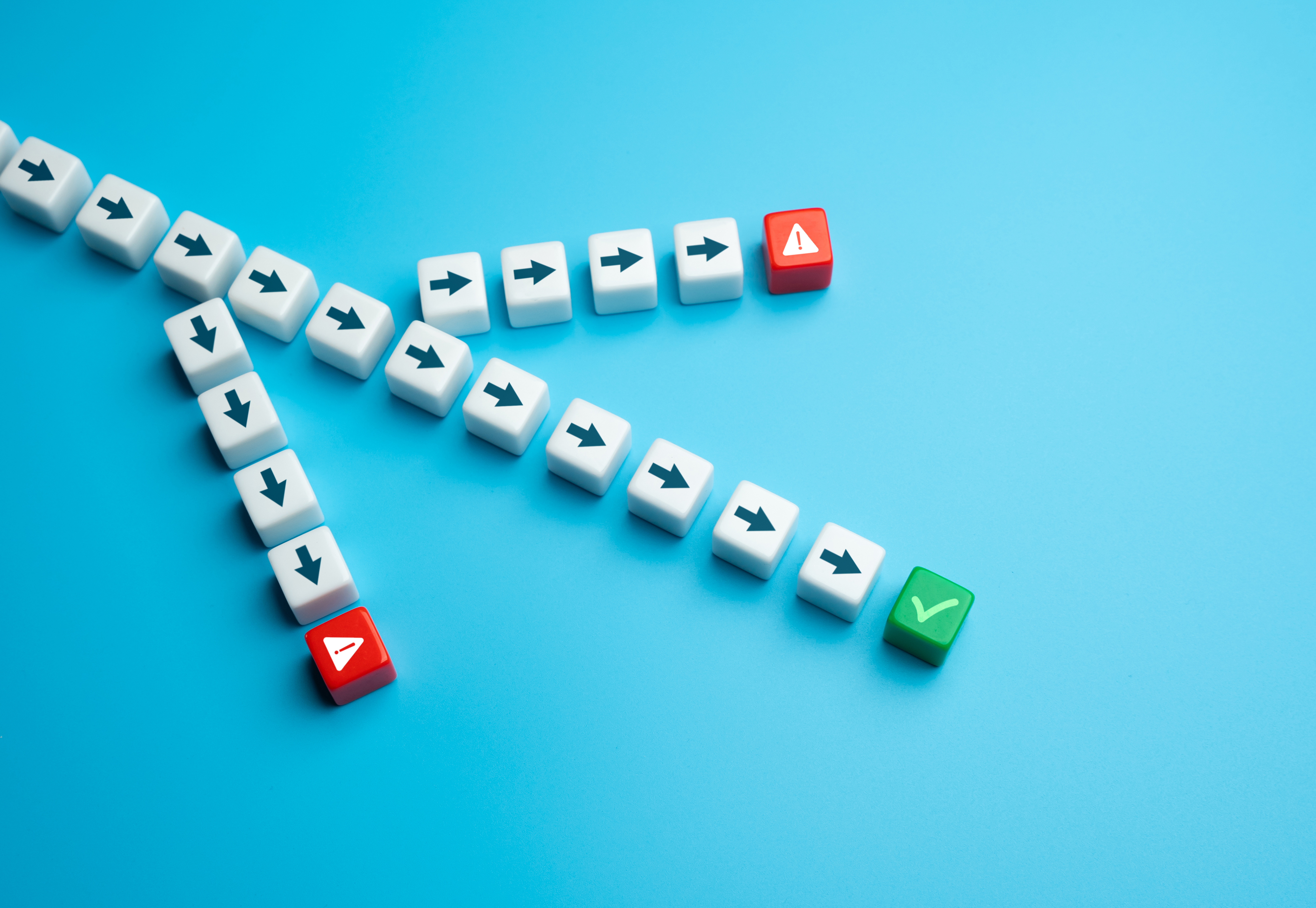
The pitfalls of a purely budget-based approach
Purchasing decisions driven solely by financial concerns can be counterproductive. Consider the harsh operating conditions in the paper industry—extreme heat, high humidity, and exposure to corrosive chemicals. These factors necessitate high-quality sensors.
Take a recent example of a company struggling with frequent unplanned shutdowns. This company opted for low budget wireless vibration sensors on a large scale. While this approach seemed economical initially, it resulted a painful implementation with little support and limited functionality once in place. The project was deemed a failure and led to the departure of the maintenance manager, conveying the risks of such low-price selection strategies.
A holistic asset monitoring strategy
Successful implementation requires a multidisciplinary approach. The best teams include:
- Predictive maintenance experts
- Certified vibration technicians
- Reliability specialists in the paper industry
- Information technology professionals
The goal is not to deploy as many sensors as possible, but to deploy them strategically. Ideally, a project begins on a small scale, with clearly defined success criteria.
Beyond sensors: the modern technological ecosystem
Modern technologies offer far more than basic data collection. The level of sensor sophistication plays a crucial role in obtaining actionable insights :
- A basic sensor provides a single vibration axis and a global level
- A high-end sensor captures three vibration axes, measures temperature, and integrates several diagnostic parameters
- Advanced sensors can transmit a full vibration spectrum and waveform for accurate remote analysis
For example, consider industrial fans installed on rooftops, which are often difficult to access during winter. Technicians can easily monitor these fans for most of the year, but winter access limitations create months of uncertainty. Deploying wireless sensors enables continuous monitoring, ensuring data availability regardless of physical barriers.
Cybersecurity is also becoming a critical aspect, especially in highly automated industrial processes.
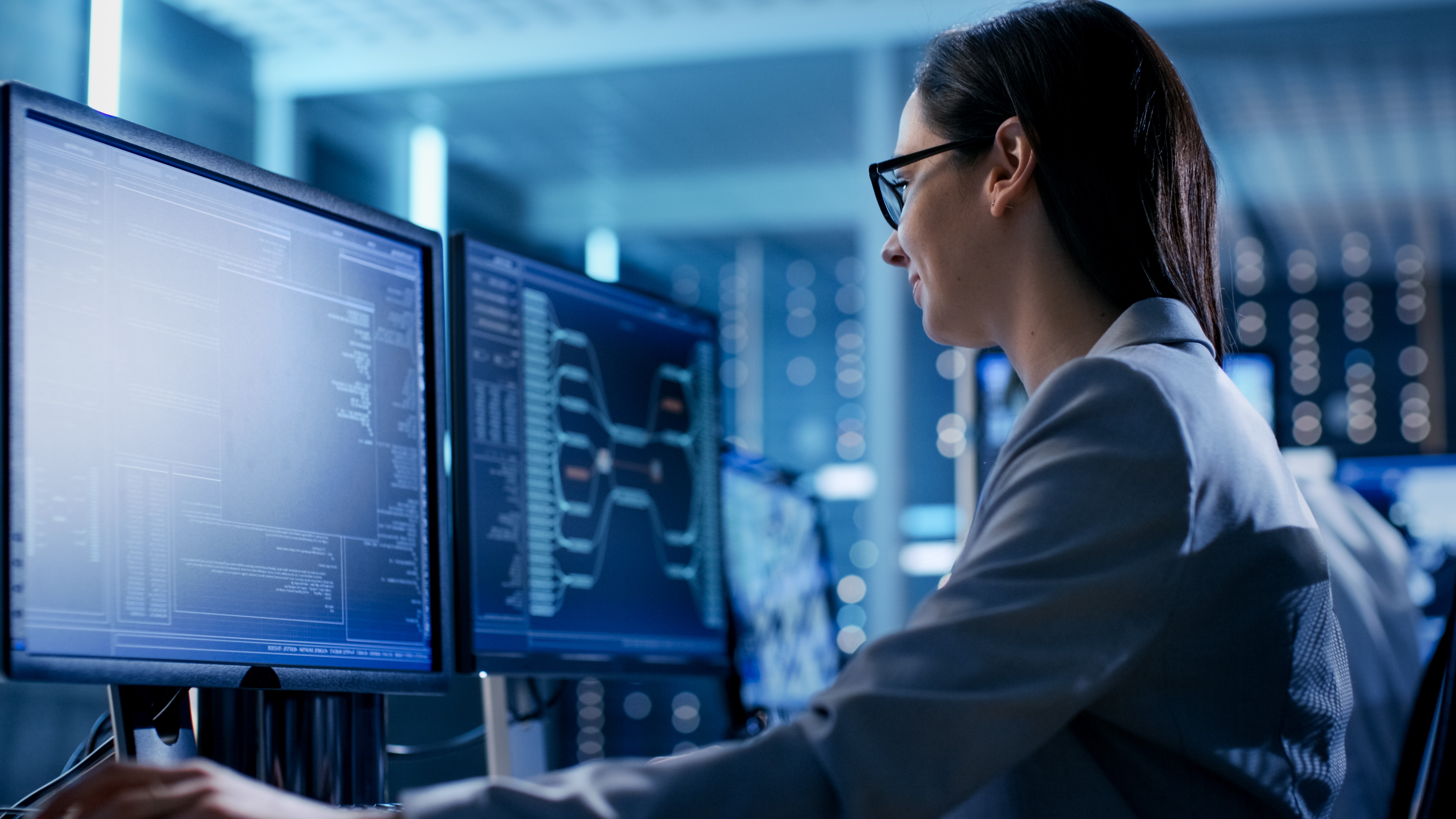
Strategic consequences of inaction
Companies that are slow to adopt these technologies expose themselves to major risks. Within the competitive paper market, underperforming facilities are often the first to close.
The benefits of a proactive approach include:
- Significant reduction in unplanned downtime
- Optimization of maintenance resources
- Reduced safety risks
- Improved performance indicators
An investment, not an expense
The return on investment (ROI) for predictive maintenance can be accurately calculated. Benefits include fewer breakdowns, automated data collection, and improved production performance—transforming monitoring into a valuable growth driver for the business.
Conclusion: Innovation as a culture
Industrial asset monitoring is more than adopting new technology—it’s a cultural transformation. It requires strategic vision, deep expertise, and a commitment to continuous improvement.
The companies that succeed will be those that see predictive maintenance not as a cost, but as a lever for performance and competitiveness.
Emerson's AMS solution tackles these challenges by improving asset reliability through predictive intelligence and integrated monitoring and diagnostic tools. It enables professionals such as reliability engineers and operational managers to make informed decisions, improve safety, productivity and efficiency, while advancing industrial innovation.
A North American leader in industrial reliability, Laurentide Controls stands out for its multidisciplinary team of over 250 reliability engineers and specialized technicians. As Emerson’s Impact Partner for Eastern Canada, we deliver world-class solutions supported by local technical expertise. Our comprehensive offerings include lifecycle services tailored to your assets, customized automation solutions, and expert guidance to optimize your operations.
Since 1968, we have been driving growth and enhancing the performance of industries across Eastern Canada. Our mission is to transform your challenges into opportunities through innovative and sustainable solutions. Discover how our expertise can advance your business towards operational excellence. Contact our specialists today.